Factory Workers and Mesothelioma
Factories, plants, mills, and foundries are places where workers have (and to some extent still do) become exposed to asbestos.
According to the U.S. Bureau of Labor Statistics, approximately 12 million people in 2020 worked in factories, plants, mills, and foundries.
Some of those 12 million may find themselves coming into contact with asbestos if their place of employment was built prior to the 1980s or if the equipment they use as part of their job was likewise made before that time.
But those factory workers are in the minority. Most who have been exposed to asbestos in factories were employed in those places at some point between the mid-1940s and around the early 1990s.
The sources of exposure could have included products the factory workers made, the machines and tools the factory workers used in making the products, and the materials that went into constructing the factory itself.
The diseases triggered by asbestos can be fought. And factory workers who were exposed to the carcinogenic mineral may have the right to use the legal system to obtain compensation to pay for the battle against those diseases.
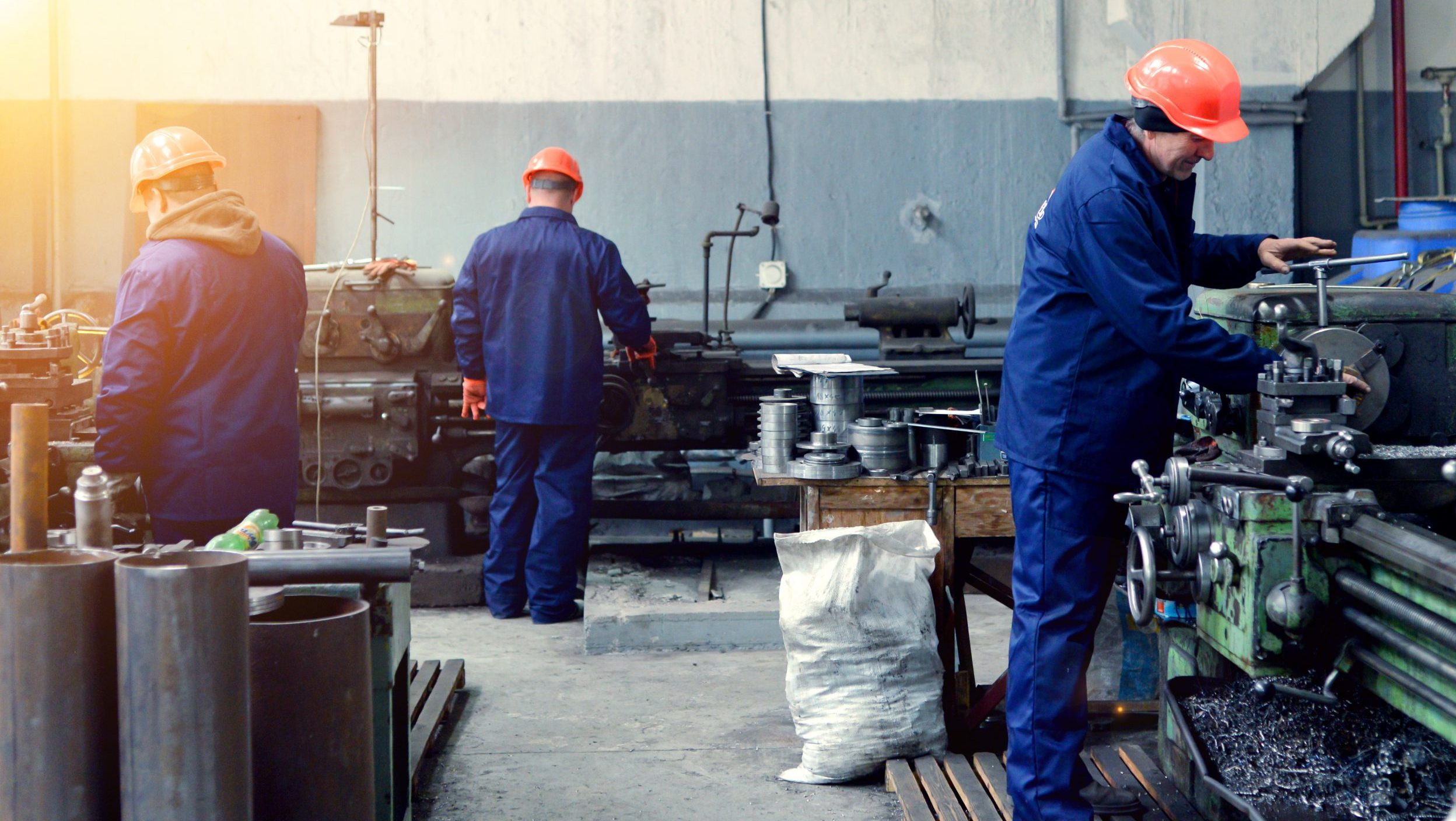
Who qualifies as a factory worker?
Among those who work in factories—and have been or can still be exposed to asbestos—are:
- Materials handlers and stagers
- Assemblers
- Sorters
- Packers
- Supervisors
- Quality control personnel
- Equipment/systems operators
- Equipment/systems repairers
- Facilities engineers and custodians
- Clerical staff
- Executive staff
Asbestos was present in many types of manufacturing businesses. These included:
- Textile mills
- Apparel makers
- Wood products fabricators
- Paper producers
- Chemical manufacturers
- Plastics and rubber products makers
- Metal goods companies
- Machinery manufacturers
- Computer and electronic product manufacturers
- Appliance producers
- Transportation equipment makers
- Furniture crafters
- Foundries
- Home-based piecemeal shops
The common thread among all these types of manufacturing businesses is asbestos. Even if the raw materials used or the products made were asbestos-free, then the mineral was likely present inside the equipment relied upon to operate the factory and possibly inside the very walls, roofs, and floors of the building in which the factory was housed.
The equipment most likely to have contained asbestos and posed a health danger to factory workers were conveyor systems, lathes, and grinding machines.
Factory workers and asbestos exposure from conveyor systems
This system is basically a long metal frame that extends from the point where production begins to the point where it ends. The product being made travels along the frame atop a belt or a series of wheels or rollers.
Some conveyance systems are designed to carry the product down the assembly line if a factory worker at one station simply pushes the product to the next station. Other conveyance systems are set up to rely on gravity to move the product down the line.
However, most conveyance systems employ electric motors to move things along.
A feature often found in powered conveyance systems (in addition to their electric motor) is a set of brakes. These serve to prevent a conveyor weighted down with many units of the product being made from slipping in the opposite direction when power to the motors is shut off.
Another feature often found in powered conveyance systems is a flexible drive belt that takes the energy produced by the motor’s spinning shaft and transmits it to the conveyor itself. (The drive belt is not the same as a transportation belt—the surface upon which the product being made sits as it’s carried along from assembly station to station.)
One other feature typical of powered conveyance systems is a clutch. The purpose of the clutch is to prevent the motors from burning out when a stopped but fully loaded conveyor is restarted (the clutch eases the reengagement between the motor and conveyor belt or wheels).
The thing about electric motors, brakes, drive belts, and clutches is they generate significant heat. Prior to the 1970s, the way that heat was dealt with was by coating or packing these components in asbestos.
Asbestos was a mineral prized for its ability to inexpensively insulate against high heat.
However, there was a problem with the use of asbestos in conveyors. It was possible for fibers of the mineral to break free and find their way into the same air that factory workers inhaled.
Asbestos fibers often broke free as a result of friction (for example, when asbestos-coated brake pads pressed against a brake drum or other metal surface to bring the conveyor to a stop there would be dislodging of some of the mineral’s particles).
Asbestos fibers also could break away from a conveyor’s components as a result of wear and tear. As asbestos-containing drive and transport belts are operated, they tend to fray or crack. That’s all it takes for the asbestos on and within them to go airborne.
Airborne asbestos can remain in enclosed factory air for many days. Anyone who breathes that air is likely to pull into his or her lungs some of those floating asbestos particles. Once inside the lungs, the fibers remain trapped. Ten or more years later, those asbestos particles can cause healthy cells to begin mutating and eventually bring about an asbestos disease such as mesothelioma.
Factory workers and asbestos exposure from lathes
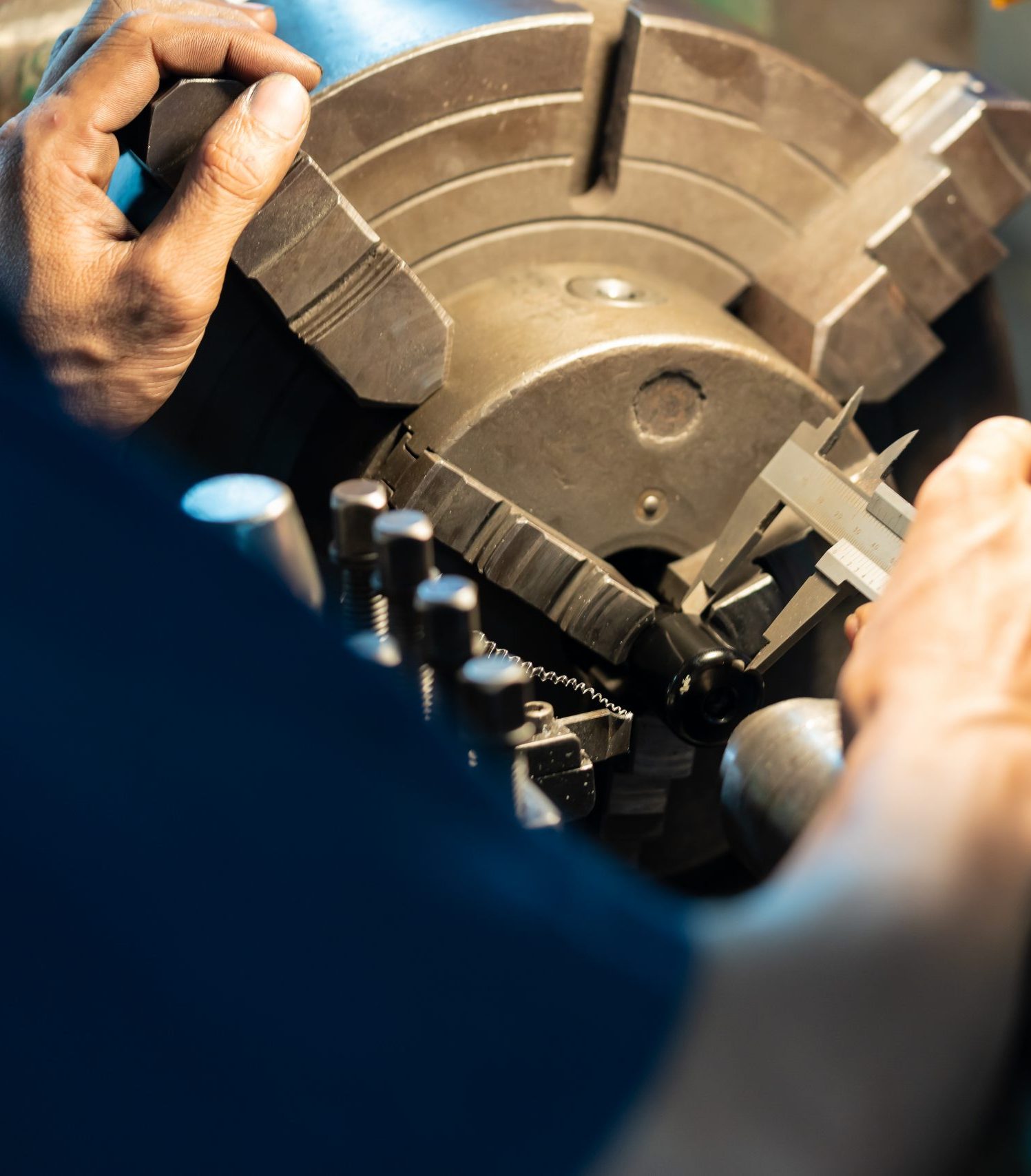
The operator of a lathe would secure the product part or piece at each of its ends by means of a clamp or collet. The lathe would then spin the secured piece at a high speed. As the piece rapidly spun, the lathe operator would gradually bring into contact with the surface of the piece a special blade or burr. This would create a small groove, indentation, or even a deep cut in the piece all the way around the axis of rotation.
Prior to the Industrial Revolution, lathes were powered by the operator’s feet or by a waterwheel in an adjacent flowing stream or river. With the coming of the Industrial Age, lathes were powered by steam engines and, later, by electric motors.
Electric motors generate high heat when operated. For that reason, it was once common practice to insulate the internal components of electric motors with asbestos inside their housings.
It was also a practice to use asbestos as an insulating material or coating for the components of the lathe that were subject to intense heat generated by the friction resulting from the high-speed spinning action.
This was problematic for operators of lathes and for other factory workers in the vicinity. The reason was that any time there was a disturbance of the asbestos used to contain heat from the lathe there existed the potential for tiny fibers of that asbestos to be released into the air.
However, asbestos could also be released into the air if the part or piece undergoing lathing happened to contain asbestos. As the lathe dug into the piece, clouds of asbestos dust would spew in all directions and be capable of traveling from one end of the factory to the other.
By whatever means asbestos entered the air, it was potentially unhealthy for the people unfortunate enough to have inhaled or ingested the particles. From these particles could decades later come mesothelioma or other asbestos-related diseases.
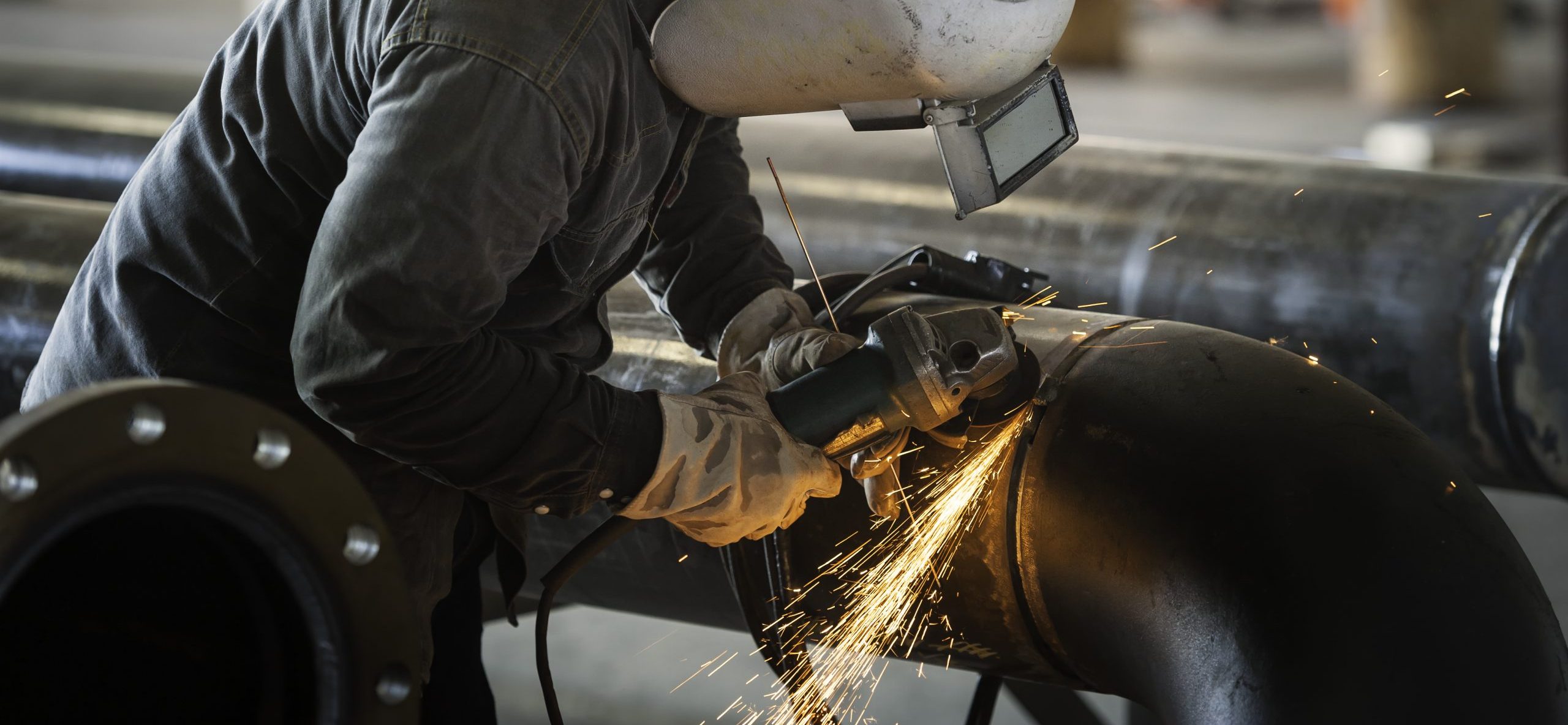
Factory workers and asbestos exposure from grinding machines.
A piece of equipment intended to accomplish that is the grinder. Many factories have grinding equipment (which can include planers, sanders, polishers, and other devices for removing excess material from parts and pieces).
A grinder is basically a rapidly spinning abrasive wheel brought into direct contact with the uneven or unfinished part or piece. The wheel chips off tiny bits of material from the part or piece, leaving behind a uniformly smooth surface.
Historically, grinders were powered by a waterwheel and, later by steam engines until the advent of electric motors in the late 1800s.
The high heat produced by electric motors was usually contained by an insulating coating or packing of asbestos. Asbestos also was used to contain the high heat generated by the spinning abrasive wheel.
Asbestos fibers tend to dislodge and enter the air when disturbed. Jostling an electric motor to service it could be sufficiently disturbing of the asbestos within a grinder. The same would be true for replacing a worn abrasive wheel with a new one or for changing over to a different type of wheel.
Asbestos could also enter the air during the process of grinding a part or piece made of asbestos. The grinding would produce asbestos dust in large quantities and enable it to circulate throughout the factory.
Asbestos circulating in the air could be breathed in or swallowed by factory workers unaware of the health dangers the free-floating mineral posed. Those dangers included the risk of mesothelioma, asbestos lung cancer, and other asbestos-related diseases.
Factory workers and asbestos exposure from raw materials and semi-finished goods
During staging, assembly, sorting, picking, quality testing, and preparation for shipment, asbestos-containing materials were vulnerable to the effects of rough handling.
Rough handling made it possible for tiny fibers of the asbestos within to break free and find their way into the air inside the factory.
Workers not wearing appropriate protective clothing—including respirators—were at risk of inhaling or ingesting those airborne asbestos particles. Once inside the body, the particles would remain there for many years and, in some cases, trigger devastating changes in the cells surrounding the lungs or intestines. The result could be mesothelioma, asbestos lung cancer, asbestosis, or other asbestos-related conditions.
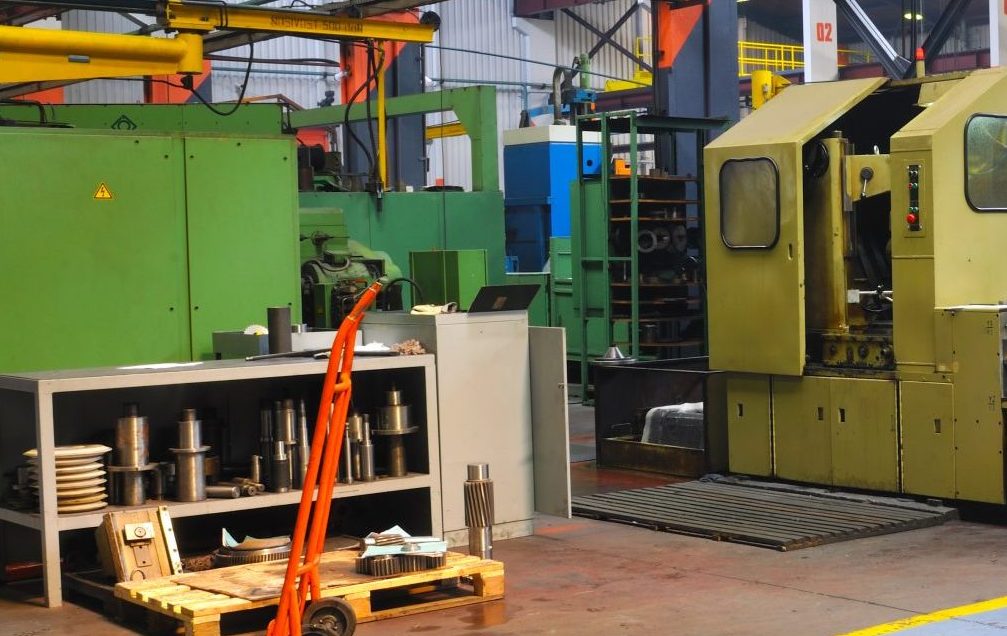
Factory workers and asbestos exposure from the factory itself
The asbestos was to be found in everything from insulation to roofing, from ceiling and floor tiles to wallboard and plumbing.
Combined with the asbestos unleashed into the air from the factory’s products and manufacturing equipment, the asbestos from the structural building materials could have exposed workers to a significant amount of the carcinogenic mineral day in and day out.
Factory workers’ rights to compensation after asbestos exposure
Perhaps you or a loved one has developed mesothelioma, asbestos lung cancer, asbestosis, or other asbestos-related disease as a result of asbestos exposure that occurred while working in a factory, plant, mill, or foundry.
You may have the option of bringing a lawsuit against the company or companies responsible for causing the asbestos exposure. If so, you might be awarded a substantial sum in compensation.
Alternatively, the company or companies being sued by you or your loved one may wish to avoid a costly trial and will instead propose a generous settlement offer out of court.
There also is a special system set up to compensate factory workers when the target of a potential lawsuit can’t be taken to court at all because that would-be defendant filed for bankruptcy protection.
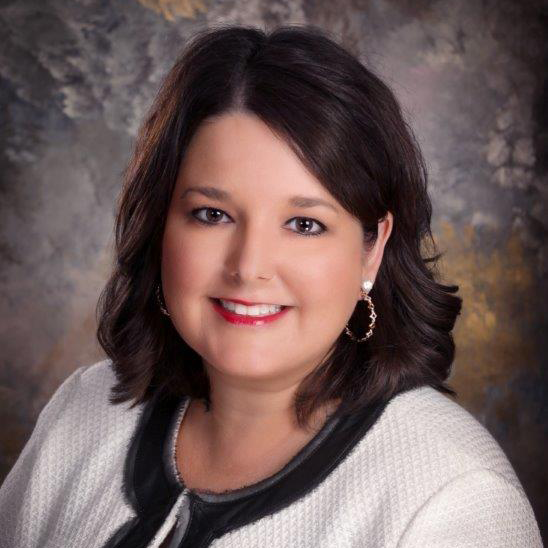
About the author…
Beth Gori graduated from the State University of New York at Buffalo in 1995 with a degree in Biology. She attended law school at St. Louis University and graduated with a J.D. and certificate in Health Law Studies in 1999.