Welders and Mesothelioma
The U.S. Bureau of Labor Statistics indicates that there are approximately 400,000 working as welders. Before them came a long parade of people who have used fire or electric arcs to join pieces of metal.
It was known to rod manufacturers decades before the 1970s that asbestos was a source of cancer and other serious diseases.
Unfortunately, those makers chose not to give adequate warning to the welders who bought and used those rods. In fact, some rod makers opted to give purchasers no warning at all. It was just easier that way. And saying nothing also didn’t harm the manufacturers’ revenues and profits.
For many who worked as welders between the 1940s and 1980s—and perhaps even as recently as the 2000s and 2010s—this failure to adequately warn resulted in asbestos exposure.
Exposure occurred each time an asbestos-containing rod was brought under the flame of an acetylene torch or the arcing current of an electric welding system. The resultant billows of smoke brimmed with asbestos particles that filled the air surrounding the welder.
Having not been adequately warned about the true nature of that smoke, welders went about their work giving little thought to what they were breathing or perhaps even swallowing.
And what they inhaled or ingested was asbestos, particles of which penetrated deep into the lungs or intestines and remained there permanently.
The harm of this would not be immediately apparent. It could take one or more decades for a disease that scientists know is caused by asbestos exposure to onset. The asbestos-related diseases a welder might develop include mesothelioma, asbestos lung cancer, and asbestosis.
Only a small percentage of asbestos-exposed welders become stricken by one of these diseases. However, those at greatest risk worked in the trade from the 1940s until around the 1980s. Welders active from the 1990s onward also are at risk, but to a lesser extent. Even welders today can encounter asbestos—not necessarily from rods (unless they are using ancient stock), but from other construction materials at a jobsite where remodeling, retrofitting, or demolition of a very old structure is taking place.
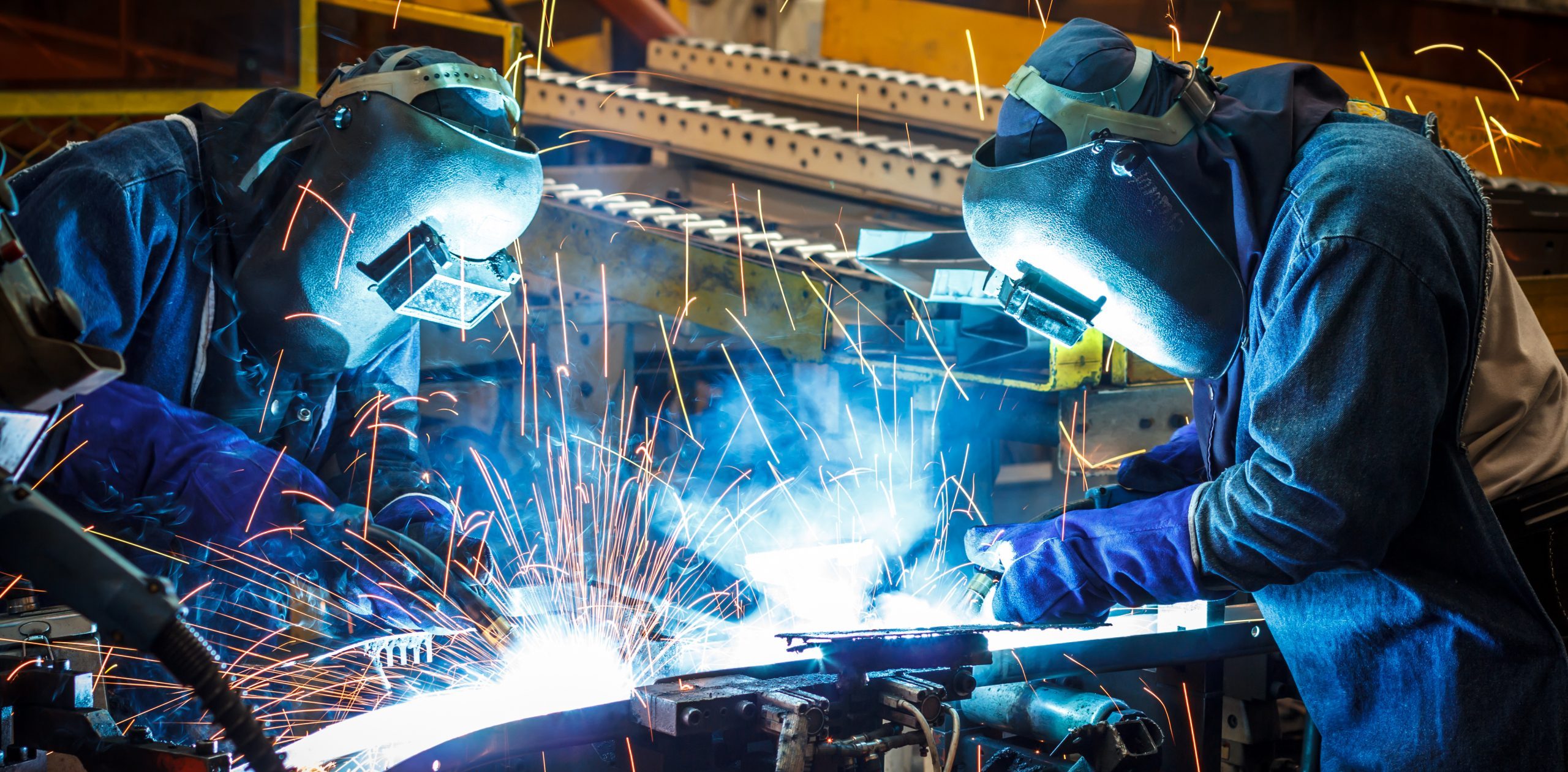
Who qualifies as a welder?
Welders work in construction but also in any industry that utilizes metal. Some of those non-construction industries include:
- Aircraft manufacturing and repair
- Automotive manufacturing and repair
- Energy
- Railroads
- Shipbuilding
A welding specialty field is cutting. Cutters use torches, plasma, or arcs to slice metal to size. Cutters are in biggest demand for demolition work, such as the dismantling of ships but also the teardown of buildings.
In construction, welders help build, refurbish, retrofit, and demolish low-, mid-, and high-rise offices as well as factories, institutions, refineries, powerplants, pipelines, and bridges.
The most widely used method of creating metal joins is arc welding. This entails applying electric current to the join. The current flows between closely positioned electrodes which causes an arc of intense light and heat (with temperatures reaching approximately 6,500 degrees Fahrenheit). The tip of a flux-coated rod placed adjacent to the arc supplies molten metal to fill the join and cause the pieces on each side to bond. The flux limits the chemical interaction of air and molten metal to prevent damage to the pieces and the join.
There are different types of arc welding and each requires its own type of welding rods. The arc welding types are:
- Metal Inert Gas Welding (MIG) and Metal Active Gas Welding (MAG)
- Shielded Metal Arc Welding
- Flux Cored Arc Welding
- Submerged Arc Welding
- Electro-Slag Welding
Welders and asbestos exposure
Throughout much of the 20th Century, it was common for manufacturers of rods to lace their products with asbestos. More than a quarter of the materials used to produce a rod could be asbestos. The exact amount varied with the rod’s intended application—for example, stainless steel rods might have 5 percent asbestos content, while general-purpose rods might have 30 percent asbestos content.
Some of the asbestos that makers added was incorporated into the metal core of the rod. The remainder was added to the flux coating. In both cases, the mineral was added to yield a cleaner, stronger, more easily achieved bond between the welded metal pieces.
But the improvements in weld performance came at a price. As the rod was consumed, the asbestos was supposed to adhere to the metal pieces and the join between them. Much of it did. But a portion did not. Instead, it spewed into the air amid the clouds of smoke produced by the welding process.
It did not help matters that welders used rods in quantity each workday. The more rods used, the more asbestos there was to be carried up into the air.
Another way asbestos could make its way into the air was after the weld had cooled and a grinder was applied to smooth it out. As the grinder’s high-RPM abrasion wheel chewed the ripples and rough spots of the join, copious amounts of fine debris would be jetted away from the work in a stream of sparks, smoke, and dust. Except it would not have been just metal filings in that stream. Also present would have been bits of asbestos. The metal filings may have dropped to the welder’s feet, but the asbestos particles would have filled the air around the welder’s head.
It was not until the 1980s that manufacturers stopped adding asbestos to their welding rods. However, the risk to welders continued long afterward because asbestos-laced rods made prior to that time were still available for sale—and continued to be until supplies were at last exhausted decades later.
Beyond rods and grinders, welders risked asbestos exposure several other ways. These included asbestos exposure from the personal protective equipment they wore, from being present at jobsites where various types of non-welding-related construction materials had been stocked, staged, or installed, and from working alongside professionals in other trades who were busy performing their own work with their own asbestos-containing materials and tools.
Welders and asbestos exposure from personal protective equipment
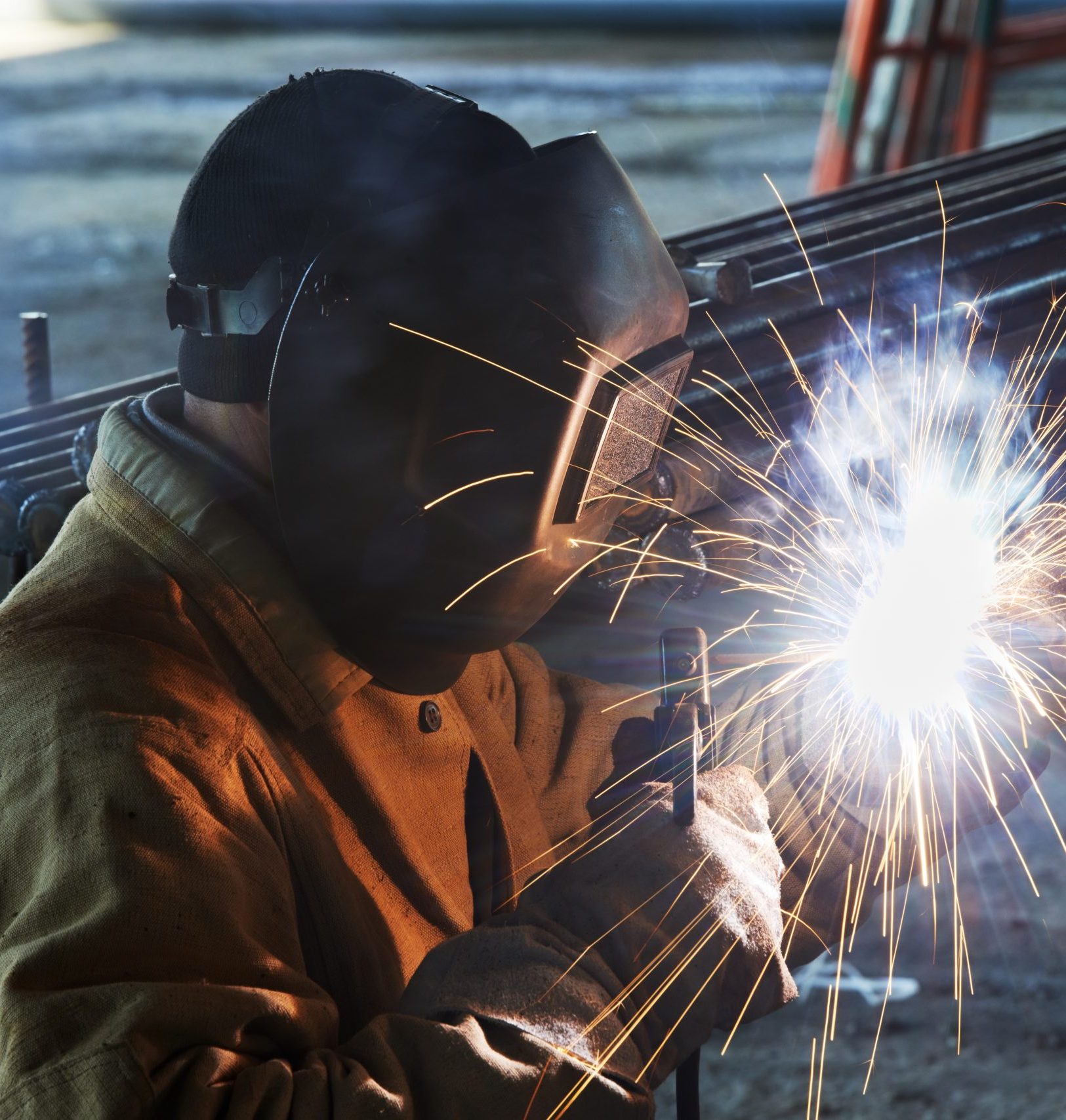
Gloves and aprons are two more pieces of personal protective equipment long relied upon by welders. For a time, these were made with asbestos woven into them. This was done to give gloves and aprons the ability to help welders stay cool and comfortable despite the extremely high temperatures mere feet or inches from their hands, arms, and torso.
As a bonus, the addition of asbestos to gloves and aprons endowed them with greater durability so they would last longer. Even so, these items were subject to wear and tear. After a while, the outer surfaces of gloves and aprons still could fray or rip. This would expose the interior material—and the asbestos particles woven into it. Some of those particles would escape into the air and be inhaled or ingested by the welder.
Welders also made use of welding blankets. These were intended to be laid over or wrapped around nearby heat sources, such as steam pipes, electrical equipment, or internal combustion motors. Like gloves and aprons, welding blanket were subject to wear and tear. When a welding blanket frayed or split, out came some of the asbestos within.
Welders and asbestos exposure from building materials
These non-painter building materials included:
- Drywall
- Insulation
- Ceiling and floor tiles
- Roofing systems
- Electrical systems
- Pipes
- Boilers and furnaces
- Bricks and mortar
Companies that made these and other products from the 1930s onward oftentimes put asbestos into them. The molecular properties of asbestos were such that the internal or external addition of the mineral to almost anything would make that material look better, work harder, and last longer.
For example, asbestos coated over steam pipes would prevent the high heat within them from conducting outward to exterior surfaces, making it safe for bare human hands to touch them without sustaining burns. Asbestos added to walls allowed them to block the transmission of noise. Perhaps most importantly, asbestos made things fireproof.
Asbestos in materials encountered by welders at jobsites was unlikely to be dangerous so long as those materials were not disturbed. In other words, if a person or object didn’t bang into the materials, there would be no disturbance of the asbestos. Similarly, if no one purposefully modified the materials (such as by cutting, hammering, or drilling), then, again, the asbestos would remain undisturbed.
However, in the event of disturbance, tiny pieces of the asbestos would be able to break free of the material to which it had been added. Those asbestos particles would find their way into the air shared by the welder (unless he or she were working outdoors where wind would carry the particles away from the welder’s immediate vicinity).
Were a welder to inhale or ingest at least some of the particles in the surrounding airspace, those tiny fibers would begin a journey to the depths of his or her lungs or intestines. At the journey’s end, those particles would embed next to healthy cells and begin a decades-long attempt to turn them into tumor cells.
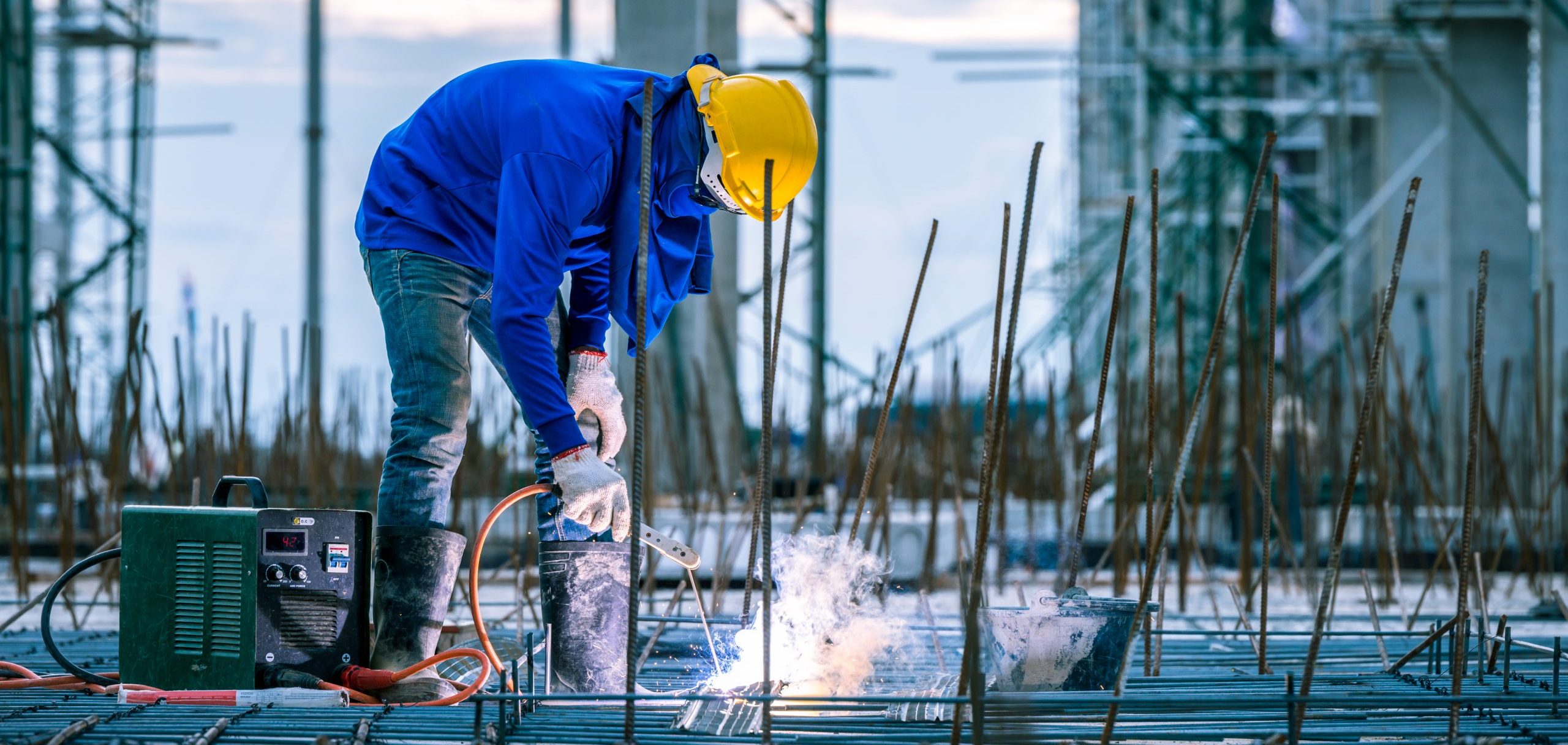
Welders and asbestos exposure from working alongside other trades
However, welders working alongside or immediately following on the heels of electricians, plumbers, bricklayers, and insulators (to name but a few) were during the era of asbestos vulnerable to exposure to the mineral as a result of the activities of those other trades.
As those other trades cut, drilled, hammered, grinded, filed, sanded, and jostled materials into position, they released asbestos particles into the air. A welder nearby might inhale or ingest some of those particles. Even if the other trades completed their work a few days before the welder arrived to begin his or hers, those asbestos particles could potentially still be present in the air—or at least available to become airborne once more in the event they settled to the ground (all it would take to send the particles aloft was for a draft to breeze through or someone to kick up a cloud by walking through the area).
Welders’ rights to compensation after asbestos exposure
Many welders so exposed and who subsequently suffered an asbestos-related illness discovered that those conditions are expensive to treat. They also discovered that developing asbestos illness can make it difficult or impossible to work and earn a paycheck.
Fortunately, asbestos-injured welders can sue to collect compensation for the cost of treatment, to make up for lost wages, and more.
Such lawsuits can be aimed at the companies that made and sold the asbestos products welders used or with which they came into contact. There is a record of plaintiff welders winning substantial sums from these lawsuits (which often never get to the trial phase, since defendant companies tend to prefer settling out of court).
Also available to asbestos-injured welders is the option of remedy from an asbestos bankruptcy trust. This is an entity set up by asbestos companies that have sought the protections of federal bankruptcy laws. Those laws bar welders and others from suing such companies, but also compel the companies to deposit large amounts of funds into trusts so that injured parties can nonetheless apply for compensation.
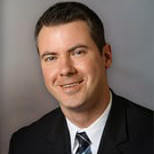
About the author…
Gregory Sandifer graduated from Southern Illinois University Edwardsville and received his law degree from Western State University College of Law in Fullerton, California.